Hyper-Fixation or Rapid prototyping?
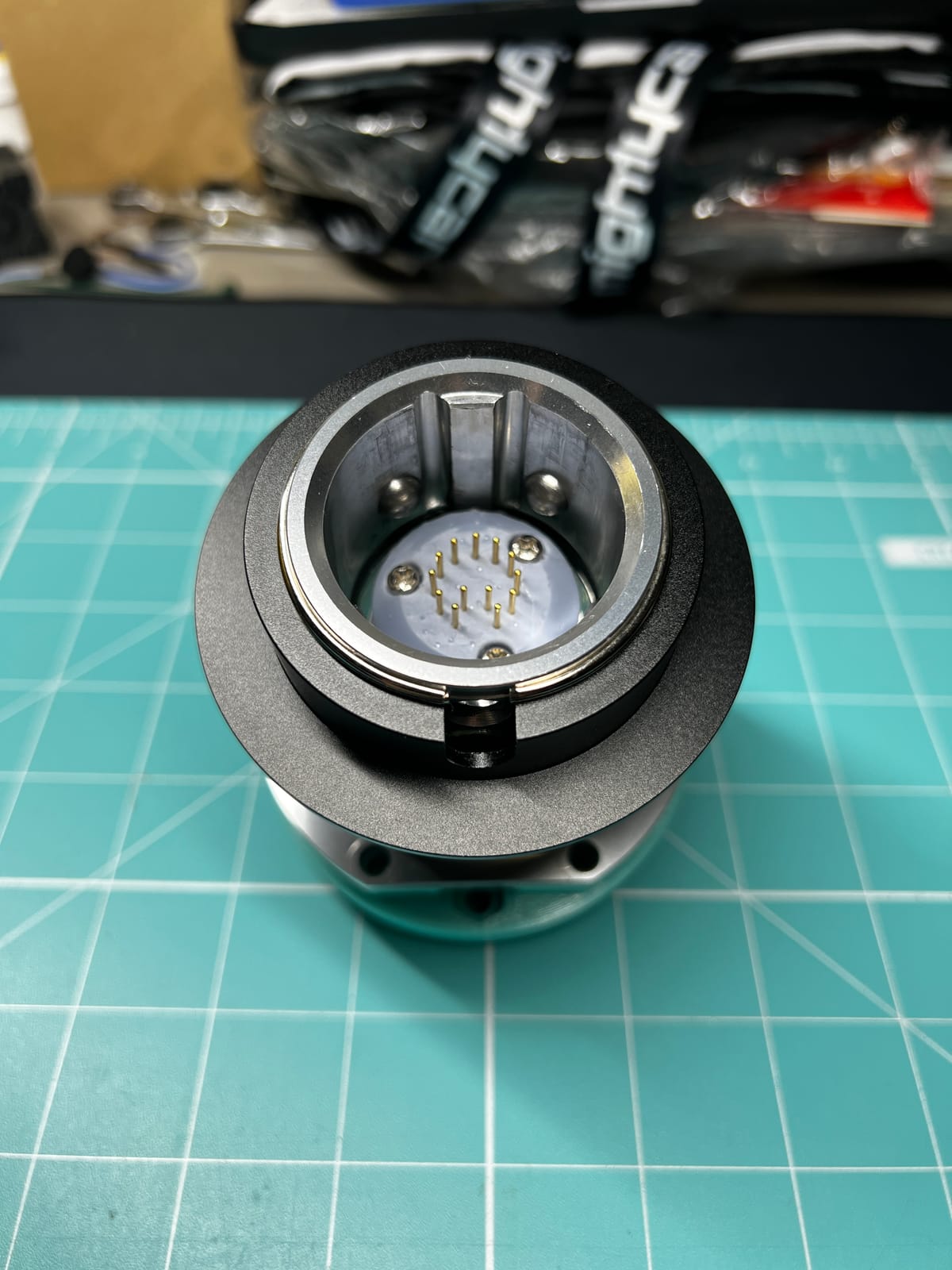
While it’s still somewhat fresh, may as well document the week of iterations I pushed out recently.
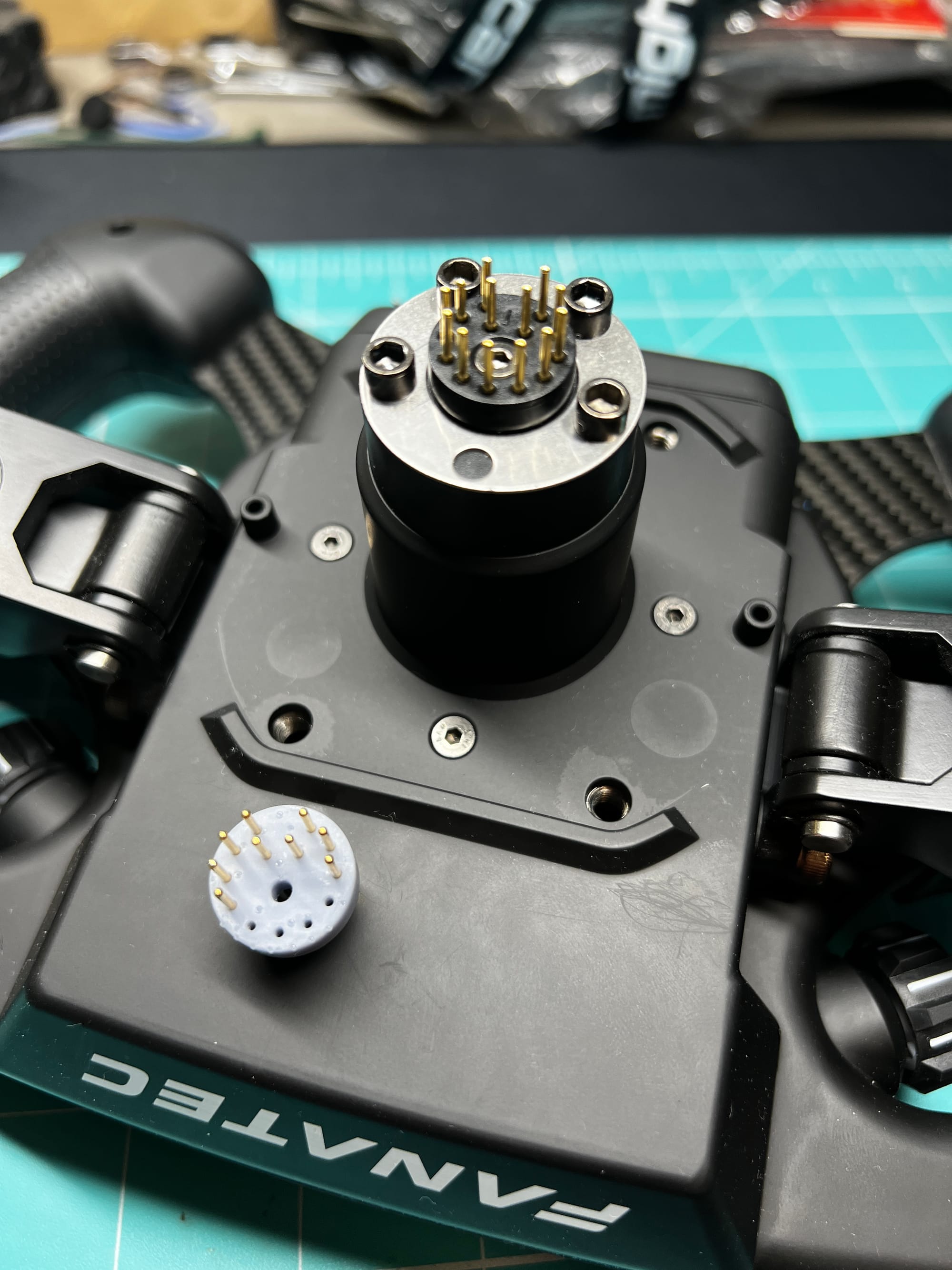
The first hurdle was getting the proprietary 13 pin connector right. I bought the Deutsch pins forever ago and attempted to create the connector using an FDM printer initially, the tolerances weren’t fine enough to line up the pins on the wheelbase. First attempt on the resin printer, the 2mm pockets were touched up with a drill bit and the pins slotted in perfectly.
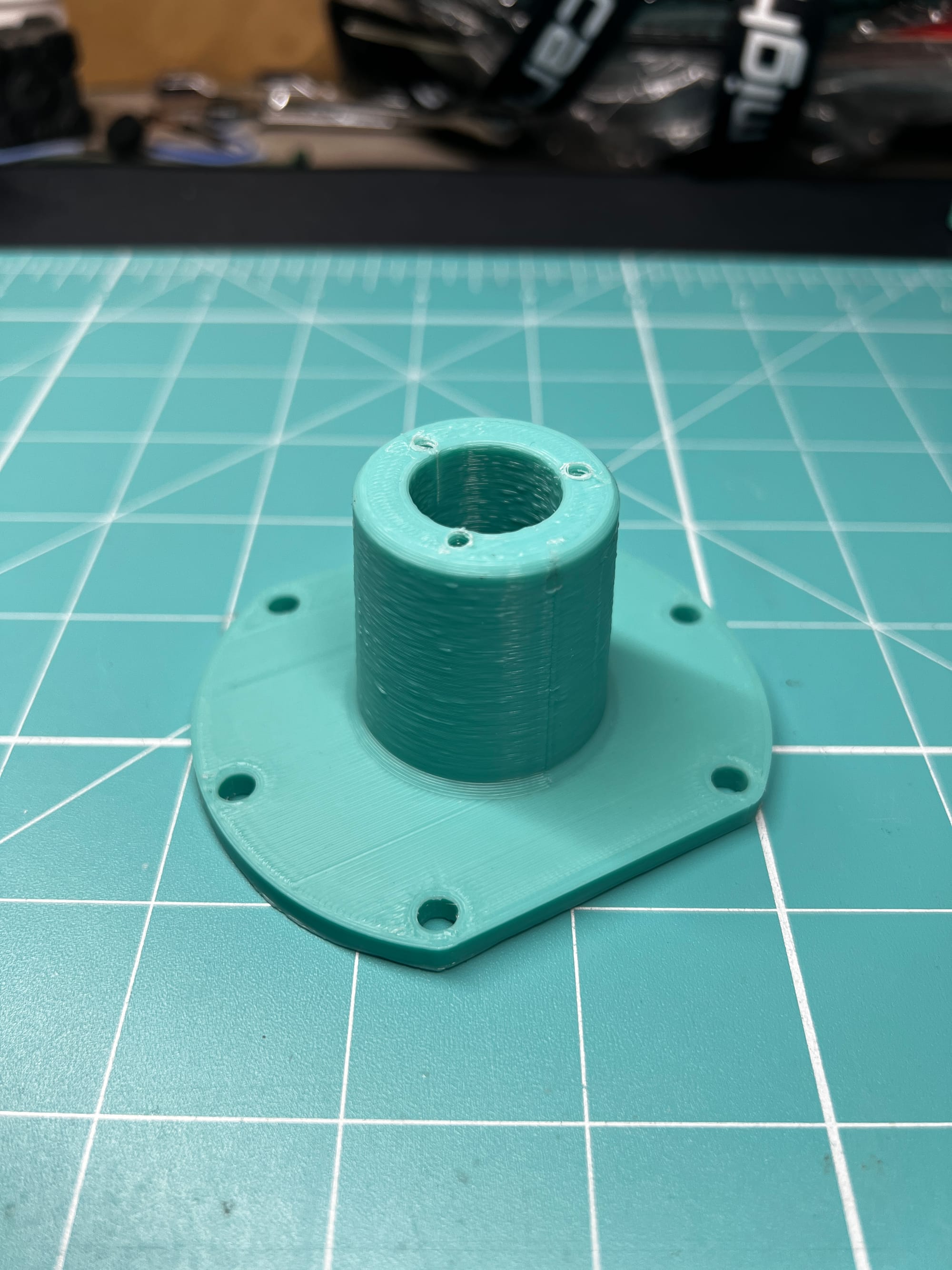
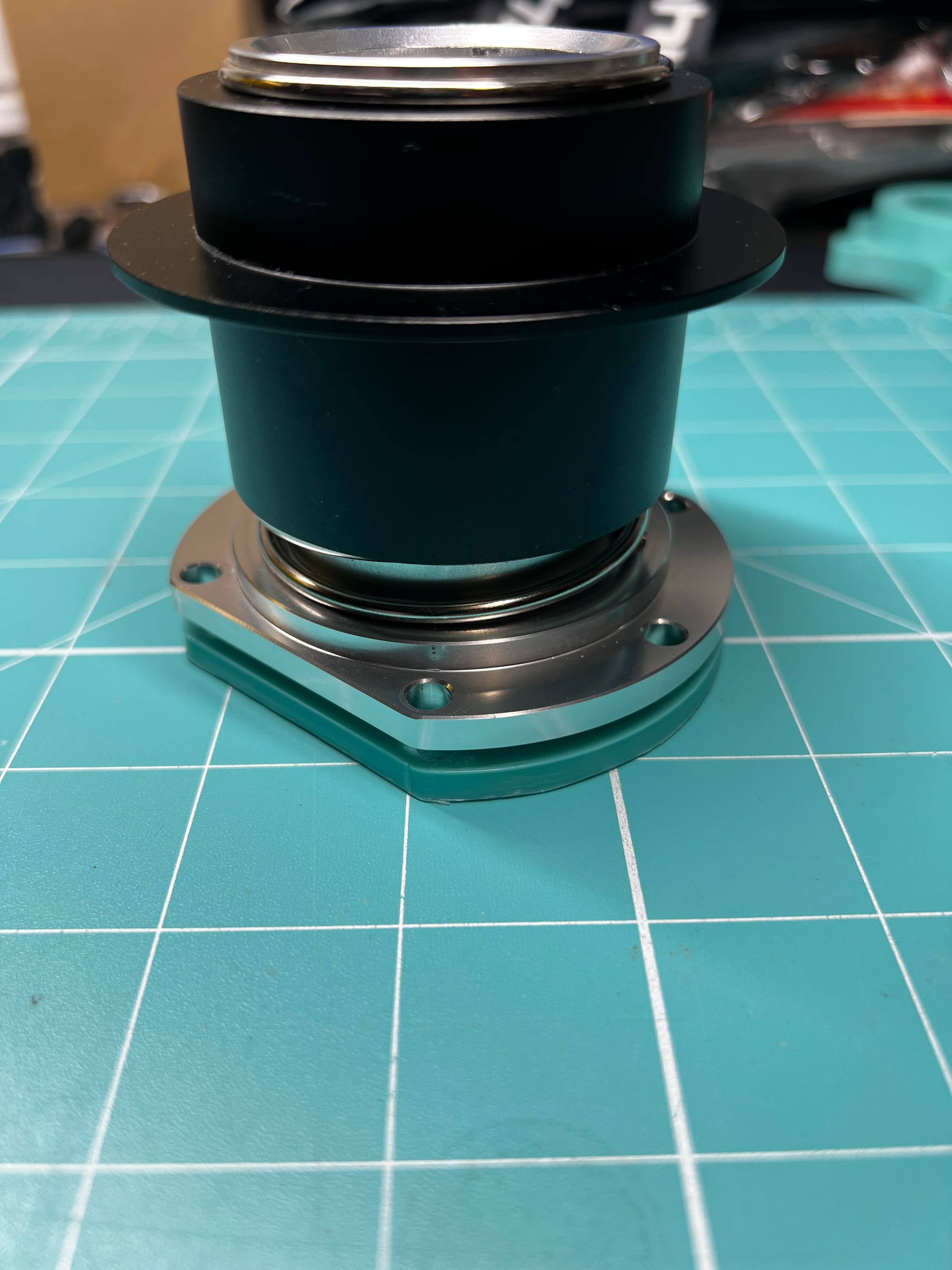
Continuing on to the snout that holds the pin connector in the quick release, I got the bolt pattern correct, but the snout was a touch too wide at the base preventing the quick release from sitting flush on the flange.
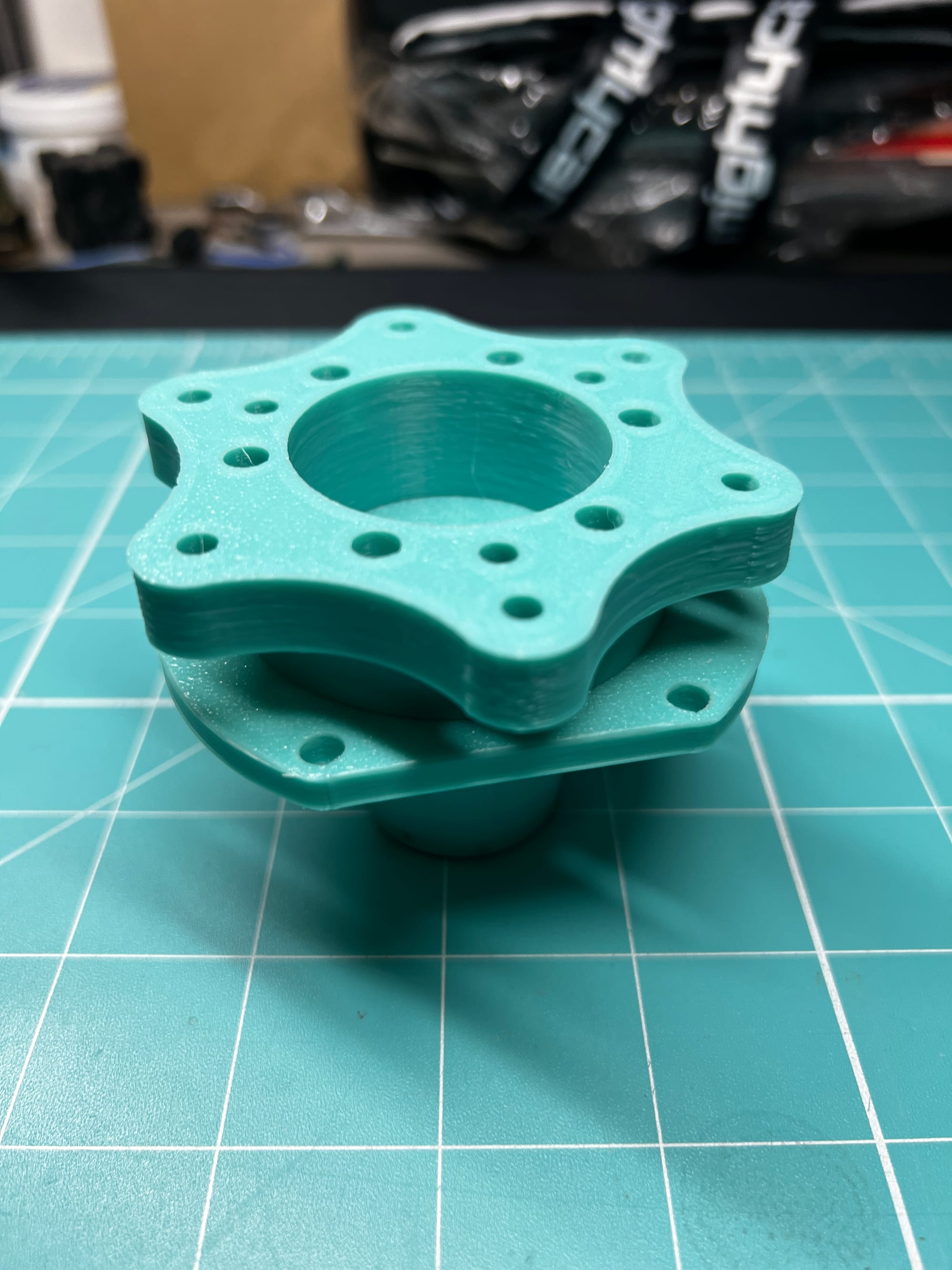
I’ve miss-placed my 2nd attempt but it was a two piece design using 6 bolts to clamp the two together similar to the configuration above. I wasn't a fan of how little material there was with only bolts holding it all together. I toyed with the idea of adding a key between the two to increase the surface area but decided to move to a one-piece design.
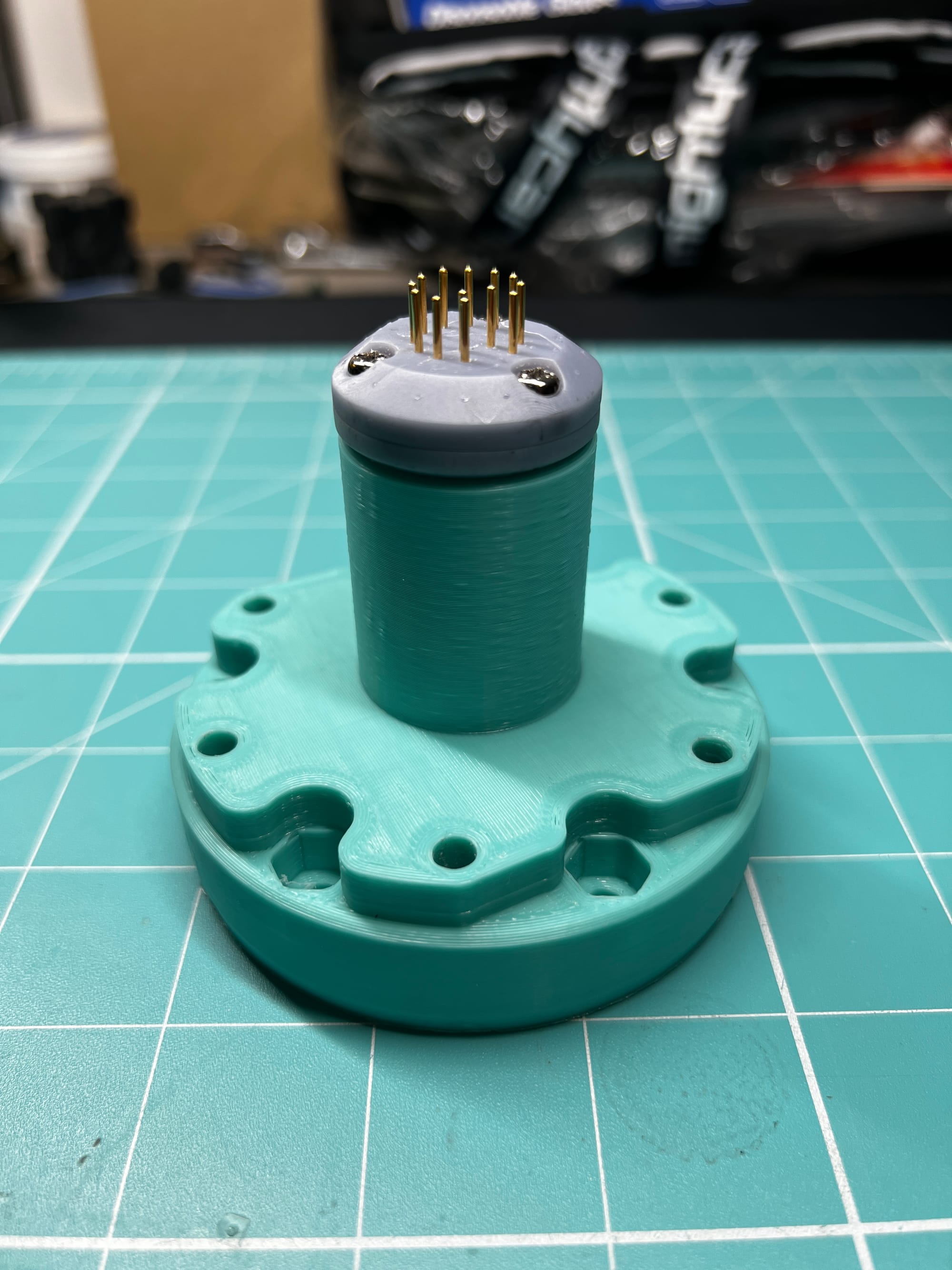
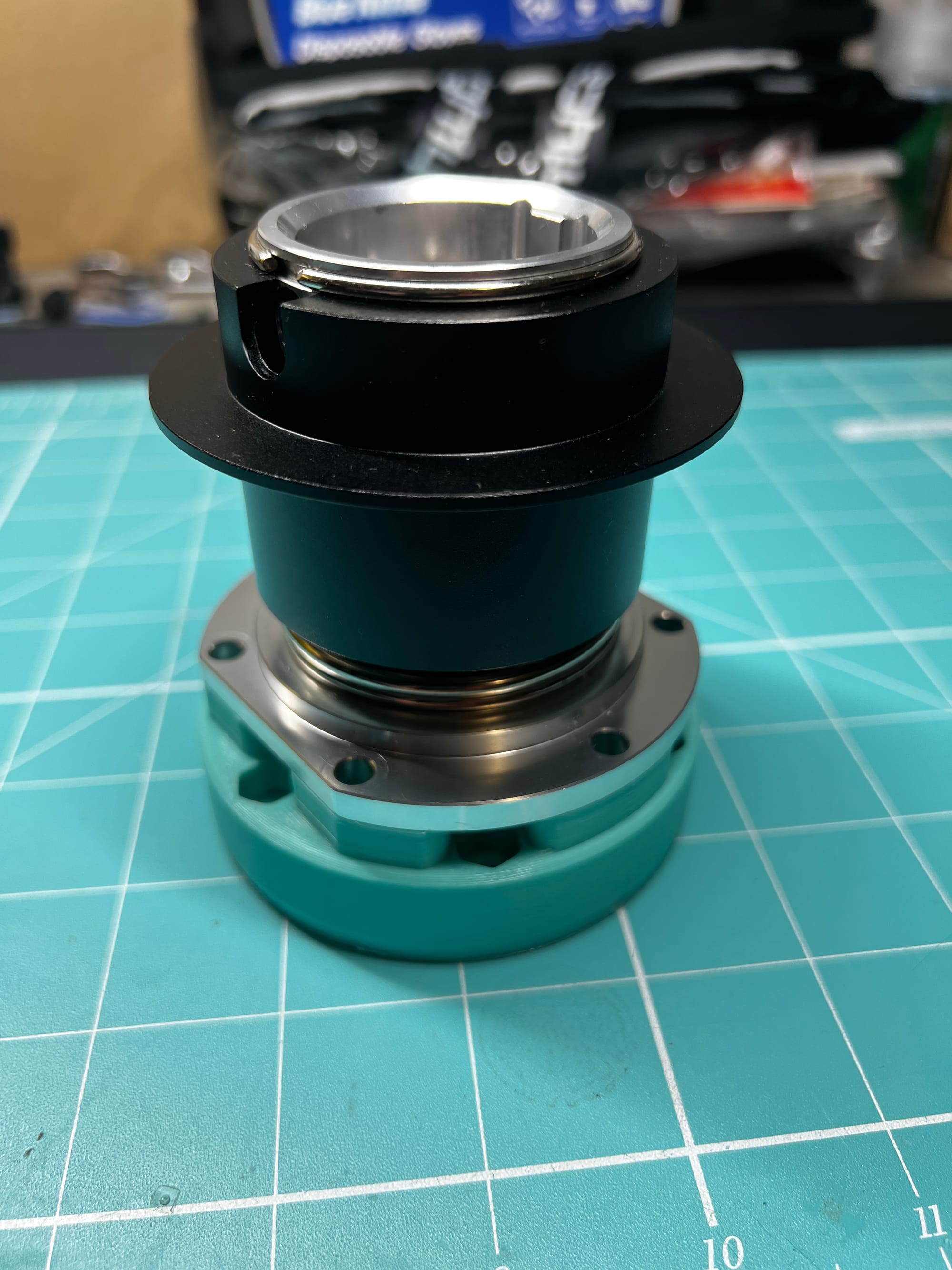
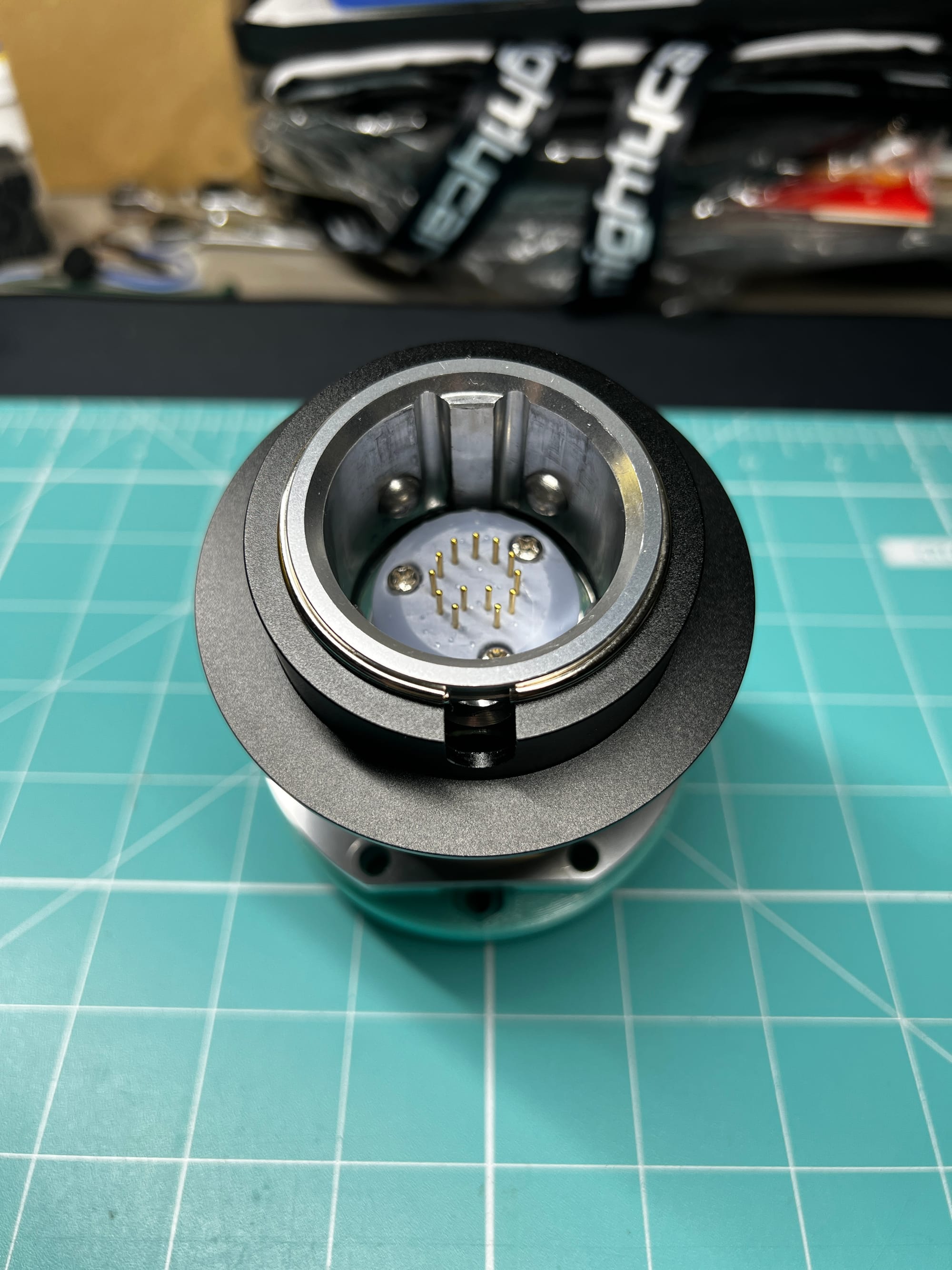
Then to the first one piece design, simplifying the design as well as adding more material in the stress zones for longevity. I’m sure the design will be perfect adequate being printed in PLA or PETG. But I’ll be sourcing quotes for aluminium cnc machining and producing moulds for compression carbon fibre (Aka forged carbon). This version is currently being reprinted as I write this. The M5 pockets in this version were too wide allowing the captive nuts to spin just not do their job 🙄...